Отечественная технология белого и цветных цементов
(К 70-летию промышленного производства белого цемента)
В.А. Кулабухов, канд. техн. наук, А.М. Дмитриев, канд, техн. наук,
Г.И. Чистяков, инж., В.Н. Кожевников, инж.,
О.К. Алёшина, инж., А.В. Шутова, инж.
ОАО «НИИЦемент»
ОАО «Щуровский цементный завод»
Реферат. В статье кратко описана история создания отечественной технологии белого и цветных клинкеров, организации промышленного производства декоративных цементов.
Отражена роль Щуровского цементного завода в проведении промышленных испытаний и внедрении разработок НИИЦемента, Гипроцемента и ряда кафедр ВУЗов страны по совершенствованию технологии производства белого цемента.
Введение
В мировой практике строительства белый и светлоокрашенные цементы широко применяются в бетонах с привлекательной однородной поверхностью, используются при изготовлении сборных бетонных наружных панелей, сборных балок и колонн, при бетонировании на месте стен зданий и сооружений, при отделке дорог и городских мостовых плиткой и камнем для мощения из декоративных цементов, а также при нанесении дорожной разметки, при возведении бордюров и тумб, барьеров безопасности и т.д.
Кроме создания выразительных элементов современной архитектуры, применение декоративных цементов обеспечивает индустриализацию отделочных работ.
В нашей стране промышленное производство белого цемента было начато в августе 1936 года и первые заводские партии отечественного белого цемента были применены при строительстве шлюзовых башен на канале «Москва-Волга», водного вокзала в Москве, первых станций московского метрополитена, театра им. Маяковского и Центрального театра Красной Армии, жилых домов на улице Горького, павильонов на ВДНХ, которые до сих пор радуют глаз людей.
Создание отечественной технологии белого цемента и организация его промышленного производства
Работы по разработке технологии белого цемента были начаты в 1929 году С.С. Череповским во ВНИЦе под руководством профессора В.Н. Юнга. Были разработаны параметры получения белого и цветных цементов, изысканы месторождения маложелезистого сырья, имевшие значение для массового производства этих цементов.
С.С. Череповским была разработана технология получения белого и цветных клинкеров, отличительной особенностью которой был созданный им способ газового отбеливания клинкера, т.е. повышения его белизны в процессе охлаждения в слабо восстановительной газовой среде, явившийся новым технологичским процессом и новым конструктивным решением в цементном производстве. Разработаны параметры газового отбеливания клинкера в процессе его охлаждения [1].
Механизм газового отбеливания клинкера заключается в уменьшении степени окисления красящих оксидов Fe3+ и Mn3+ до Fe2+ и Mn2+ и образовании устойчивых соединений:
Fe2O3 ® Fe3O4 и Mn2Оз ® Мn3О4.
Это сопровождается значительным повышением белизны и коэффициента яркости цементов, и что очень важно, устранением слабо зеленоватого оттенка в маложелезистом клинкере и цементе (при содержании оксидов железа до 0,5 % и марганца до 0,02 %), который для архитектурных целей считается холодным и нежелательным тоном, и который обусловлен, как было установлено Э.И. Нагеровой [1], именно содержанием марганца в карбонатном компоненте.
Исследования карбонатных пород цементных заводов и вновь разведанных месторождений показали, что содержание оксидов марганца колеблется в них от тысячных долей процента до 0,02 - 0,04, реже 0,07 %. Исключением является уникальный пресноводный известняк-травертин Араратского месторождения в Республике Армения, отличающийся полным отсутствием оксидов марганца при минимальном содержании оксидов железа - до 0,1%.
Очень важно отметить, что после газового отбеливания клинкеров с повышенным содержанием оксидов железа - 0,7 - 1,5 – 2 % и выше, как было установлено в полупромышленных, а затем и в промышленных условиях, получаются цветные клинкеры и цементы от светло-кремового до желтого – чистого цвета, чистых тонов, равноценные по цвету цементам, получаемым совместным помолом маложелезистого белого клинкера с добавкой от 1 до 5 - 7 % природных красковых руд.
По постановлению Правительства об организации производства белого цемента и приказу Наркомтяжпрома в феврале 1936 года для организации промышленного производства белого цемента и выпуску промышленной партии объёмом 25 тыс. т. был выделен Таузский цементный завод в Азербайджанской Республике.
В течении всего пяти месяцев бригадой Гипроцемента под руководством С.С. Череповского и коллективом Таузского цементного завода были проведены работы по подготовке оборудования и цехов, площадок для привозного сырья, организации технологического контроля производства нового вида цемента, внедрению ускоренных и новых методов химического анализа, оптического метода определения белизны цемента, обучению и подготовке сменных химиков, инструктажу мастеров и рабочих ведущих профессий завода. Заключены договоры на поставку сырья ранее изученных институтом месторождений: маложелезистых известняков Араратского (Республика Армения) и Щуровского (Московская область) месторождений, белых глин Часов-Ярского и Просяновскго месторождений (Республика Украина), диатомита Кисатибского месторождения (Республика Грузия) и красковых руд - охры Журавского месторождения (Воронежская область) и сурика Криворожского месторождения (Республика Украина). Проведены испытания по выпуску промышленной партии белого цемента.
Применение чистейшего известняка Арарратского месторождения, отличающегося полным отсутствием оксидов марганца, позволило получить цементвысокой белизны, выше 80 % по BaSO4, без отбеливания клинкера, а лишь при умеренном опрыскивании водой клинкера, выходящего с обреза вращающейся печи.
Постановление Правительства было выполнено в срок - к 1 августа 1936 г.
После успешного выпуска первых промышленных партий белого цемента Таузский цементный завод был переведен на постоянное производство белого и цветных (светлокремового, кремового, бежевого, жёлтого, розового, красного, зелёного, синего и чёрного) цементов. Качество цементов отвечало высоким требованиям: по белизне, прочности (марка 400, 500), сопротивлению истиранию, цветостойкости, долговечности [1, 2]. Араратский известняк все годы применялся на Таузском цементном заводе для получения белого цемента.
Академик А.В. Щусев, приехав на строительство здания института им. Маркса - Энгельса - Ленина в Тбилиси и увидев первые образцы белого и цветных цементов заводского помола, высоко оценил их качество, особо отметив, что для архитекторов важно иметь цементы трех основных цветов - белого, желтого, красного.
Главнейшие объекты строительства того времени в Москве, Ленинграде, Сочи, Новосибирске и других городах страны были обеспечены отечественным белым цементом, что позволило избежать ввоза его из-за границы.
Были разработаны ГОСТ 965-41 на белый цемент, шкала цветных цементов, согласованная с архитекторами, и инструкции по производству и применению белого и цветных цементов.
В 1940 году на Таузском цементном заводе при участии Гипроцемента был смонтирован опытно-промышленный холодильник-отбеливатель в комплекте с газогенераторной установкой. Однако генеральные испытания отбеливателя, в связи с угрозой нападения Германии на нашу страну и срочным переводом Таузского завода на производство тампонажного цемента для бакинских нефтепромыслов, были короткими.
Клинкер с температурой около 1000°С с обреза вращающейся печи поступал в отбеливающий холодильник, в котором создавалась бескислородная слабовосстановительная газовая среда, получаемая путем сжигания генераторного газа. В восстановительной среде клинкер охлаждался до 300°С. Испытания показали работоспособность конструкции отбеливателя, выявили некоторые недостатки её, подтвердили точность установленных параметров отбеливания и ожидаемое изменение цвета клинкера в зависимости от содержания оксидов железа, а также значительное увеличение белизны и коэффициента яркости цементов. При газовом способе отбеливания из маложелезистого клинкера, содержавшего 0,35 - 0,4 % оксидов железа на араратском известняке был получен белоснежный цемент, характеризовавшийся коэффициентом яркости 85 – 90 %. Из клинкера для тампонажного цемента, содержавщего около 3 % оксидов железа, получился цветной клинкер и цемент чисто желтого цвета (без добавки охры) с коэффициентом яркости 67 % против 32 % до отбеливания.
Через три года после окончания Великой Отечественной войны производство белого цемента в Таузе было возобновлено и после частичной замены изношенного оборудования мощность Таузского цементного завода была удвоена по сравнению с первоначальной и доведена до 35 тыс. т белого цемента в год.
Более 30 лет, вплоть до закрытия в 1980 г., Таузский цементный завод обеспечивал белым цементом многие стройки страны.
Организация промышленного производства белого цемента на Щуровском заводе
В первые годы после окончания войны Гипроцементом были проведены работы по реконструкции старого законсервированного Щуровского цементного завода и переводу его на производство белого и цветных цементов (по предложениям, разработанным институтом ещё в 1934 году) на базе местного известняка, привозного песчано-глинистого компонента и мазута, который в 1957 г. заменили на природный газ.
Холодильник был реконструирован и оснащён газогенератором. Схема и технология производства были сохранены в том же виде, как на Таузском заводе. Работы по монтажу отбеливающей установки и пуску завода осуществлялись силами завода при участии бригады НИИЦемента в составе С.С. Череповского и О.К. Алёшиной.
Несмотря на отрицательное заключение НИИЦемента о технологии водного способа отбеливания клинкера, по указанию Главзападцемента МПСМ СССР срочно было смонтировано устройство для отбеливания водой клинкера, выгружаемого прямо из зоны спекания вращающейся печи с температурой порядка 1400°С в ванну с проточной водой. Для сушки клинкера специально был смонтирован сушильный барабан с топкой, работающей на мазуте.
Сравнительные испытания двух способов отбеливания клинкера были проведены в июле 1953 г. на шламе одного состава.
При газовом отбеливании клинкер во всей массе имел однородный кремовый цвет, характерный для данного содержания оксидов железа - 0,7 % и марганца - 0,03 %. Рабочие, прошедшие стажировку, уверенно обслуживали газогенератор. Газовое отбеливание клинкера в про цессе его охлаждения после выхода из печи обеспечивало и удобство регулирования процесса обжига, и полноту процесса клинкерообразования.
Испытания водного отбеливания показали, что выгрузка клинкера из зоны спекания печи помимо большого расхода топлива и потери тепла и воды, сопровождалась неоднородной гранулометрией и степенью обжига клинкера, что обусловливало колебания в содержании свободной извести, белизны и прочности цемента.
Клинкер выходил из водяной ванны с влажностью около 10 %, а после сушки, как показал опыт, такой клинкер сохраняет остаточную влажность 0,2 - 0,5 %, которая снижает размалываемость и белизну цемента. Мелкие гранулы имели слегка зеленоватый оттенок.
Измельчение сравниваемых клинкеров в заводской мельнице осуществлялось в равных условиях - металлическими телами, что снижает эффект отбеливания на 5 - 7 % абс. Коэффициент яркости цементов, при этом, из клинкеров, отбеленных газом и водой, получился практически одинаковым: 69 – 71 % при удельной поверхности 2760 см2/г и 71 - 72 % при более высокой удельной поверхности - 3240 см2/г.
После измельчения в фарфоровой ступке коэффициент яркости цемента до отбеливания составил 61 %, после отбеливания газом - 75 - 78 %. Эти результаты показали целесообразность применения в мельницах для помола белого клинкера неметаллических мелющих тел и футеровки для исключения присадки железа .
Несмотря на положительные результаты пусковых испытаний и явные преимущества газового способа отбеливания по технологическим, экономическим и качественным показателям, отмеченные также в заключении проф. докт. техн. наук В.В. Кондакова, по указанию Главка газовый отбеливатель был остановлен на ходу под предлогом предовращения возможного взрыва и отравления персонала, а завод переведён на водный способ отбеливание клинкера.
В действительности конструкция отбеливающего холодильника при соблюдении инструкции по его эксплуатации исключала отравление персонала и взрыв газовой смеси, что было подтверждено заводскими испытаниями.
Внедрение технологии газового отбеливания на Сас-Тюбинском заводе
С переводом в стране большинства промышленных предприятий на природный газ, были разработаны совершенные экзотермические установки для получения восстановительного газа.
В 1967 году в соответствии с приказом Министра ПСМ СССР И.А. Гришманова о развитии производства декоративных цементов, НИИЦементом были даны заключения о пригодности сырья для производства белого и цветных цементов на Сас-Тюбинском заводе. По проекту для этого завода, выполненному Гипроцементом, были разработаны технические требования на проектирование и изготовление газового отбеливателя в комплекте с экзотермической установкой ЭК-250, согласована конструкция газового отбеливателя с ВИИЦеммашем.
Первая технологическая линия на этом заводе с применением газового способа отбеливания была пущена в 1969 г.
В 1982 г. была закончена реконструкция трех технологических линий Сас-Тюбин-ского завода По оценке Министра ПСМ Казахской ССР Б.П. Паримбетова, в технологии производства декоративных цементов была решена важная задача: впервые на этом заводе внедрён эффективный метод отбеливания клинкера в бескислородной слабовосстановительной газовой среде [3].
Выпуск высококачественных белого и цветных цементов достиг 400 тыс.т в год, и они отгружались почти во все райны страны.
В период 1996 – 1997 гг. и в 2002 г. Састюбинский цементный завод – ныне предприятие ОАО «Састобе Цемент» - временно не работал, производство было возобновлено в 2003 г. Сегодня завод производит белый портландцемент марки М500 по ГОСТ 965-89, который применяется в Республике для производства сухих строительных смесей, производства белого и цветных бетонов и блоков, тротуарных и облицовочных плиток, цветного шифера и т.д. [4].
Разработаный способ газового отбеливания клинкера создал предпосылки для массового производства в цементной промышленности страны дешёвых белых и цветных клинкеров и цементов на базе местного сырья ряда действующих заводов.
Промышленные испытания на Щуровском заводе отбеливающего холодильника, оснащённого экзотермической установкой, и опыт эксплуатации отбеливающих холодильников на трёх технологических линиях Сас-Тюбиского завода с 1969 года и на Енакиевском заводе в Украине по настоящее время показали их надёжность в работе.
Совершенствование технологии водного способа отбеливания клинкера
Исследованиями технологии белого цемента с применением водного способа отбеливания занималась группа научных сотрудников кафедры вяжущих НПИ - Новочеркасского политехнического института (ныне Южно-Российский государственный технический университет) под руководством докт. техн. наук, профессора И.Ф. Пономарева.
Коллектив Щуровского завода при участии бригады этого института во главе с канд. техн. наук А.К. Грачьяном посвятили много лет и творческих сил освоению и усовершенствованию водного способа отбеливания клинкера [ 5, 6].
Этими исследованиями было установлено, что повышения белизны клинкера можно достигнуть при увеличении содержания в нём алита, обладающщего меньшей способностью растворять оксиды железа по сравненю с белитом. А для интенсификации обжига трудноспекаемой сырьевой смеси следует вводить минерализаторы, например, Na2 SiF6 [7].
Ими было также показано, что эффективным способом получения клинкера высокой белизны, является создание восстановительной газовой среды при обжиге, которая существенно изменяет состав его железосодержащей фазы [7].
Исследованиями НПИ также было подтверждено, что весьма важным является процесс отбеливания клинкера при его охлаждении. Для экономии топлива при обжиге белого клинкера НПИ был предложен вместо водного способ отбеливания клинкера путём кратковременного воздействия на выходящий из зоны спекания раскалённый клинкер водяного орошения и природного газа. В условиях такой обработки клинкер охлаждается до температуры 500 – 400оС, что исключает необходимость специальной сушки [8].
Лабораторией обжига НИИЦемента в процессе исследований были неоднократно усовершенствованы конструкции водяного отбеливателя. В итоге, на Щуровском заводе для снижения времени контакта с водой клинкера, выходящего из зоны спекания, вода стала подаваться в специальные полые лейки, а газ – для создания восстановительной среды – непосредственно в слой клинкера. При этом происходила интенсивная конверсия газа в присутствии паров воды с выделением активных восстанавливающих агентов – водорода и оксида углерода, обуславливающих, наряду с резким охлаждением, повышение белизны клинкера, что улучшило процесс отбеливаниия [ 9 – 11].
Немаловажное значение в технологии производства белого цемента, и по данным исследований НПИ и НИИЦемента, имеют условия помола сырьевых материалов и клинкера. По рекомендациям этих институтов для уменьшения присадки железа необходимо применять неметаллические мелющие тела и футеровку мельниц, что, в свою очередь, требует ввода эффективных интенсификаторов помола.
Наиболее надежным решением для сохранения потенциальной белизны клинкера является измельчение его в струйной мельнице, разработанной в НИИЦементе, в которой полностью исключается присадка в белый цемент металлического железа. Это было установлено работами в НИИЦементе под руководством В.И. Акунова [12].
Создание новых способов обжига и отбеливания клинкера и их промышленная реализация
Для производства белого цемента из-за специфических особенностей технологии характерны повышенные энергетические затраты по сравнению с производством обычного серого портландцемента. Особенно остро стоит вопрос интенсификации процесса теплообмена в зоне декарбонизации вращающейся печи, где потребляется свыше 2000 кДж / кг клинкера (или свыше 478 ккал / кг клинкера). Многочисленные исследования скоростного обжига дали основание полагать, что ускорение процесса декарбонизации позволит ускорить процесс клинкерообразования в печи и положительно повлиять на интесификацию процессов отбеливания клинкера.
С этой целью в НИИЦементе была проведена большая работа по разработке новых способов обжига клинкера, позволяющих повысить эффективность работы вращающихся печей для производства клинкера белого цемента путём обеспечения высокой скорости декарбонизации в псевдоожиженном слое, резкого локального нагревания и охлаждения клинкера в процессе отбеливания и дальнейшей его сушки, проводимых внутри вращающейся печи [11].
Автором этой работы – В.А. Кулабуховым - был разработан новый способ обжига клинкера белого цемента с ускоренной внутрипечной декарбонизацией сырьевого обжигаемого материала путём псевдоожижения его слоя продуктами сгорания топлива и регулирования газовой среды в этом слое и по длине печи и устройство для его осуществления (Авт. свид. № 841227). Установлены его параметры и создана конструкция встроенного кальцинатора псевдоожиженного слоя.
Исследованиями созданного встроенного кальцинатора, установленного в полупромышленной вращающейся печи Ø 1,25 × 16 м было установлено оптимальное соотношение расхода топлива, подаваемого в горелки кальцинатора и в главную горелку вращающеся печи: близко к 1 : 4 (при расширенной зоне декарбонизации). При этом, наряду с повышением производительности печи на 30 – 40 % достигается снижение удельного расхода топлива на 10 -15 % и теплового напряжения в зоне спекания на 15 – 20 %. Резкое нагревание материала на 200 - 300 оС при слоевом сжигании топлива в кальцинаторе ускоряет процесс декарбонизации в 4 – 5 раз по сравнению с обжигом в печи без кальцинатора, повышает белизну клинкера на 3 – 5 % и его активность на 15 – 95 кг / см 2.
На основании полученных результатов полупромышленных исследований был разработан и впервые в промышленных условиях испытан встроенный кальцинатор на вращающейся печи мокрого способа производства размерами Ø 3,2/ 2,7 × 62 м Щуровского цементного
завода [13]. На рис. 1 показан общий вид промышленной печи со встроенным кальцинатором.
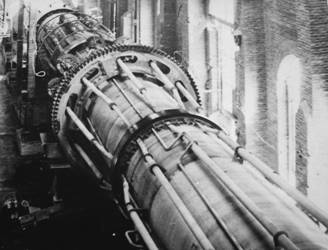
Рис. 1. Общий вид печи Ø 3,2/ 2,7 × 62 м со встроенным кальцинатором на Щуровском заводе
При работе вращающейся печи со встроенным кальцинатором в слой материала подавалось 15 % газа от общего его расхода.
Основные показатели сравнительных испытаний вращающейся печи Ø 3,2/2,7 × 62 м до и после оснащения её встроенным кальцинатором приведены в табл. 1.
Одним из основных преимуществ оснащения вращающейся печи встроенным кальцинатором является значительное увеличение скорости и степени декарбонизции. Увеличивается производительность печи, стабилизируется тепловой режим обжига, повышается стойкость футеровки в зоне спекания (достигнуто повышение стойкости футеровки почти в 2 раза) и значительно увеличивается долговечность цепной завесы. Значительно снижается общий потенциал температур по длине печи вследствие ускорения твёрдофазовых реакций в результате высокой скорости декарбонизации в зоне кальцинатора и в зоне активной диссоциации глинистых компонентов в результате выброса активного оксида кальция, образовавшегося в псевдоожиженном слое, в основной газовый поток печи и присадки его в зоне диссоциации глинистых минералов.Таблица 1
Результаты промышленных испытаний вращающейся печи со встроенным кальцинатором
Показатели |
Вращающаяся печь |
без встроенного кальцинатора |
оснащённая встроенным кальцинатором |
Удельный расход топлива, кг усл. топлива / т клинкера белого цемента |
431 |
369 |
Белизна клинкера по фотометру, ед. |
74 |
78 |
П. п. п. на входе в кальцинатор, % |
21,0* |
21,42 |
П. п. п. на выходе из кальцинатора, % |
19,0* |
12,18 |
Содержание
CO в отходящих газах, % |
2,5 |
0,2 |
Температура отходящих газов, о
C |
445 |
415 |
Производительность печи, т / ч |
5,2 |
5,6 |
Активность клинкера, кгс / см 2 |
475 |
501 |
*
Для печного агрегата без встроенного кальцинатора в аналогичной зоне по длине печи
Ускорение реакций клинкерообразования позволило снизить удельный расход топлива на обжиг клинкера более чем на 10 %, дало возможность уменьшить тепловое напряжение в зоне спекания на 25 %, повысить производительность печи на 8 - 10 % и белизну клинкера более чем на 4 %.
Разработана методика теплового расчёта встроенных реакторов-кальцинаторов с использованием методов термодинамики необратимых процессов, учитывающая одновременное протекание процессов тепло- и массообмена и физико-химических превращений (диссоциации карбонатов) как в их совокупности, так и во взаимном влиянии друг на друга [14].
Указанная методика применена при расчёте и разработке технической документации встроенного реактора-кальцинатора для вращающейся печи длиной 118 м Щуровского завода и может быть использована для разработки типовых проектов конструкций встроенных кальцинаторов для мощных вращающихся печей размерами Ø 4,5 × 170 и 5,0 × 185 м..
Принципиальное конструктивное решение встроенного кальцинатора позволяет оснащать им вращающиеся печи, работающие на любом виде топлива – газообразном, жидком, твёрдом, а также сжигать в нём топливосодержащие отходы [15].
Промышленные исследования процесса обжига белого клинкера во вращающейся печи, оснащённой встроенным кальцинатором и водяным отбеливателем, показали, что температуру в зоне спекания достаточно держать на уровне 1370 - 1380оС при обжиге сырьевых смесей с КН до 0,93 и силикатным модулем до 4,2.
С целью повышения белизны клинкера во всех режимах обжига поддерживалась восстановительная среда в зоне спекания путём изменения количества вторичного воздуха, так как продукты неполного сгорания газа в зоне спекания можно дожечь в «холодной» зоне встроенного кальцинатора. При содержании
Fe 2O 3
до 0,45 % и обычном водном отбеливании обеспечивается получение белого клинкера второго сорта с К
до более 75 % и активностью 500 кг / см 2.
В результате этих исследований выяснилось, что печь, оснащённая встроенным кальцинатором, имеет резерв по повышению белизны клинкера и можно по-новому организовать процесс отбеливания клинкера. Было установлено, что повышение белизны клинкера может быть достигнуто путём локального повышения температуры клинкера на 70 – 80о
С перед входом его в охладительную часть отбеливателя с дальнейшим резким охлаждением водой при максимальном ограничении доступа кислорода.
Для решения этих задач было разработано несколько способов, устройств и конструкций отбеливателей. В результате исследований, полупромышленных и промышленных испытаний было установлено, что оптимальной конструкцией характеризуется комбинированный газоводяной отбеливатель с сушкой клинкера внутри печи. Принципиальное отличие этой конструкции комбинированного отбеливателя состоит в том, что после перегрева в присутствии восстановительной среды клинкер резко охлаждается путём распыления воды под давлением. Доступ кислорода к клинкеру в переходный момент от перегрева к охлаждению практически сведён к нулю. Излишнее количество пара, образующегося в печи при охлаждении клинкера, удаляется посредством парозаборного зонта, системы паропроводов и пароотсосного вентилятора в атмосферу.
В результате экспериментальных исследований были установлены оптимальные технологические параметры комбинированного газоводяного отбеливателя
Полупромышленные эксперименты с использованием белых
портландцементных клинкеров Щуровского и Сас-Тюбинского цементных заводов, а также шламов, приготовленных на основе сырьевых материалов этих предприятий показали, что новый способ отбеливания клинкера позволяет
получать цемент с белизной на 3 - 5 %
выше, чем при водном способе отбеливания.
Было установлено, что при увеличении содержания оксидов железа в клинкере относительная эффективность нового способа отбеливания клинкера повышается. Полупромышленные опыты с клинкерами рядового состава цементных заводов Подольского, «Коммунар», Белгородского, Воскресенского,
Брянского, Здолбуновского, Бахчисарайского, Амвросиевского,
подтвердили этот вывод.
Физико-механические испытания цементов, полученных из отбеленных новым способом клинкеров показали, что такие цементы имеют пониженную водопотребность, нормальные сроки схватывания и около 75 % испытанных цементов из клинкеров рядового состава
показали повышение прочности в 28-суточном возрасте от 90 до 210 кг / см2, а для
белых клинкеров это повышение составило 40 – 80 кг / см2. Это объясняется не
только образованием благоприятной
мелкокристаллической структуры клинкера, но и изменением его фазового состава с образованием новой алюмосиликатной фазы переменного состава.
Внедрение комбинированного способа отбеливания на Щуровском заводе
На основании результатов лабораторных исследований и полупромышленных испытаний НИИЦементом под руководством канд.техн наук В.И. Жарко совместно с работниками Подольского
цементного завода (канд. техн. наук В.Г. Базалевского и др.) была разработана опытная конструкция устройства для отбеливания клинкера непосредственно в горячем конце вращающейся печи. Конструкция прошла испытания на вращающейся печи Подольского цементного завода, где были подтверждены результаты исследований НИИЦемента. Вместе с тем конструкция отбеливателя требовала доработки в части повышения её работоспособности (парозаборников, газовых горелок отбеливателя). Вопросами механики и теплотехники нового отбеливателя занималась лаборатория обжига НИИЦемента, а вопросами технологии – лаборатория спеццементов [16].
В июне 1982 г. на Щуровском заводе вращающаяся печь № 2 размерами 3,3/3,0/3,3´97 м была оборудована новым отбеливающим устройством. Активное участие во внедрении отбеливателя принимал главный инженер Щуровского завода В.Я. Островлянчик.
Опыт эксплуатации печи показал
следующее:
- снизилась температура отходящих газов на 20 - 30°С;
- уменьшилась температура в зоне декарбонизации на 70- 80°С;
- переместилась на несколько метров вглубь печи зона спекания;
- улучшилось свечение факела и видимость в печи;
- производительность и удельный расход топлива остались без изменения.
Заводу были рекомендованы оптимальные технологические параметры отбеливания клинкера, при которых обеспечивается получение достаточно отбеленного и охлажденного клинкера с нулевой влажностью. Зависимость белизны клинкера (Кдо) от расхода воды при его охлаждении показана на рис. 2.
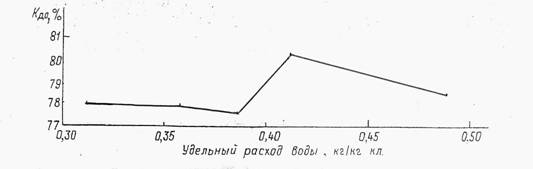
Рис. 2. Зависимость белизны клинкера от расхода воды при его охлаждении до 130 -150оC
Контроль качества обжигаемого
клинкера осуществлялся заводской лабораторией по принятой на предприятии схеме. Анализ полученных данных
показал, что в подавляющем большинстве случаев белизна клинкера, отбеленного новым способом, по сравнению с клинкером, отбелённым в воде, была на 1 – 2 % выше (табл. 2).
Определяли также белизну клинкера в зависимости от фракционного состава. Оказалось, что наиболее высокой белизной обладают фракции клинкера 5 - 30 мм.Поэтому заводу было рекомендовано организовать отсев
фракций клинкера более 30 мм и удалять их при помоле белого цемента.
Таблица 2
Зависимость белизны клинкера от КН, содержания Fe2O3 и режима отбеливания
КН
|
Отбеливание водное |
Отбеливание комбинированное |
Содержание
Fe2O3, % |
Кд.о., % |
Содержание
Fe2O3, % |
Кд.о., % |
Печь № 2 |
0,79 |
- |
- |
0,86 |
77,0 |
0,80 |
0,76 |
75,0 |
0,81 |
76,3 |
0,81 |
0,82 |
74,0 |
0,83 |
77,0 |
0,82 |
0,82 |
76,0 |
0,85 |
76,4 |
0,83 |
0,86 |
75,3 |
0,83 |
76,0 |
0,84 |
0,89 |
73,8 |
0,90 |
76,7 |
0,85 |
0,85 |
76,5 |
0,86 |
77,0 |
0,86 |
0,87 |
76,0 |
0,89 |
75,3 |
0,87 |
0,85 |
75,1 |
0,84 |
76,3 |
0,88 |
- |
- |
0,86 |
77,0 |
0,89 |
0,93 |
73,0 |
|
- |
Сравнительные
физико-механические испытания среднесуточных проб клинкеров показали, что при новом способе отбеливания размалываемость клинкера повышается на 15 - 20 %. Прочностные характеристики цементов в возрасте 28 суток были одинаковыми.
Отбеленный новым способом клинкер, минуя передел сушки, стал подаваться непосредственно на помол цемента, в результате чего сократилась численность персонала, обслуживающего сушильное
отделение, уменьшился расход топлива, улучшилось качество отбеливания
клинкера.
Основное преимущество комбинированного отбеливателя заключается в том, что клинкер второго сорта можно получать из некондиционного сырья с содержанием оксидов железа выше 0,35 %.
Положительные результаты отбеливаниия клинкера комбинированным способом, полученные на печи № 4 Щуровского завода, позволили реконструировать ещё три печи на Щуровском заводе, две печи на Састюбинском заводе, работающем на газе и две печи, работающие на мазуте, на Ангренском заводе в Республике Узбекистан. Способ и устройство комбинированного отбеливателя защищены авторскими свидетельствами СССР [9]. Внедрение отбеливателя позволило заводам получить в 90-е годы прошлого века миллионные прибыли.
Комбинированные отбеливатели эксплуатируются на двух вращающихся печах Щуровского завода до настоящего времени.
Производство белого цемента в России сегодня
Даже в трудные годы перестройки, когда спрос на белый цемент упал и исследовательские институты были практически лишены финансирования, исследования по совершенствованию технологии производства белого и цветных цементов продолжали развиваться [17, 18]. В связи с истощением сырьевой базы и повышением содержания оксидов железа в известняках до 0,5 – 0,7 % в 1997 – 1998 гг. на Щуровском цементном заводе были проведены производственные испытания Южно-Российским государственным техническим университетом по механическому обогащению известняков с использованием инерционных грохотов [17]. В обогащённом известняке содержание Fe2O3понизилось до 0,12 %, что позволило получить клинкер с содержанием Fe2O3
0,45 % и КО 83 %, в то время как КО клинкера, полученного из необогащённого известняка составлял 75 %.
В связи с ограниченностью у нас в стране запасов маложелезистого природного сырья продолжает оставаться актуальной разработка эффективных способов нейтрализации окрашивающего влияния оксидов железа. В результате исследований, проведенных в Южно-Российском государственом техническом университете [18] и установленной зависимости белизны клинкера от распределения железа по фазам при неравновесной кристаллизации найдены пути для разработки эффективных способов управления распределением Fe2O3
по клинкерным фазам в процессе обжига и охлаждения клинкера белого цемента и получении цемента достаточно высокой белизны даже при высоком содержании
FeO3(1,2 – 1,5 %) в клинкере.
В ОАО «НИИЦемент» совместно с АООТ «Цемдекор» коллективом авторов под руководством докт, техн. наук В.И. Шубина разработана технология получения белого портландцементного клинкера при использовании в составе сырьевой смеси отходов химической промышленности [19, 20].
Химический состав подобранных сырьевых компонентов, высокая их дисперсность и наличие комплекса минерализаторов обеспечивают высокую реакционную способность сырьевой смеси и позволяют значительно снизить затраты на подготовку сырьевой смеси.
Опытные партии белого цемента были выпущены на полупромышленной технологической линии мокрого способа опытного производста АООТ «Цемдекор».
Химический состав приготовленных в полупромышленных условиях сырьевых смесей (табл. 4), и минералогический состав обожжённых в полупромышленной вращающейся печи при температуре 1370 – 1460о
C клинкеров (табл. 5) с применением водного и воздушного отбеливаниия предопределили высокую белизну полученных на их основе цементов. Таблица 4
Составы сырьевых смесей при использовании вторичного сырья
№ сме-
си |
П.п.п., % |
Содержание оксидов, % |
КН |
n |
p |
SiO2 |
Al2O3 |
Fe2O3 |
CaO |
MgO |
1 |
37,20 |
14,80 |
2,30 |
0,19 |
42,50 |
0,30 |
0,93 |
5,94 |
12,10 |
2 |
37,52 |
15,0 |
0,98 |
0,10 |
43,40 |
0,25 |
0,99 |
13,90 |
9,80 |
Полученные партии белого клинкера размалывали совместно с гипсом или с гипсом и модификатором, некоторые партии клинкеров размалывали совместно с гипсом и минеральной добавкой.
Результаты физико-механических испытаний опытных партий белого портландцемента, приведенные в табл. 6, показывают, что получен высококачественный белый клинкер с активностью 540 кг / см 2 и выше. Белизна отбелённого клинкера (КДО) - 80,2 – 86,9, что соответствует I сорту белого портландцемента по ГОСТ Р 965 «Цементы декоративные. Технические условия».
Таблица 5
Минералогический состав опытных белых клинкеров
Показатель |
Белый клинкер № 1 |
Белый клинкер № 2 |
Водное отбеливание |
Водное отбеливание |
Воздушное отбеливание |
КН |
0,89 |
0,98 |
0,98 |
n |
4,78 |
6,0 |
7,17 |
p |
11,5 |
9,31 |
9,77 |
Fe2O3
, % |
0,40 |
0,25 |
0,30 |
CaOсв., % |
следы |
2,31 |
1,68 |
Минералогическикий состав по данным рентгеновского анализа |
C3S ± 1,5 % |
67 |
78 |
77 |
C2S ± 3 % |
25 |
13 |
13 |
C3A ± 0,5 % |
2,8 |
5,5 |
7,0 |
C4AF ± 0,5 % |
нет |
<1 |
<1 |
CaOсв.
± 0,5 % |
нет |
1,5 |
2,0 |
Таблица 6
Результаты физико-механических испытаний опытных партий белого цемента
№ п/п |
S, см 2/г |
Нормальная густота, % |
Сроки схватывания, час-мин. |
В / Ц |
Расплыв конуса, мм |
Активность, кг / см 2 |
Белизна |
Начало |
Конец |
Цементы на основе клинкера с КН = 0,89 отбелённого в воде |
1 |
4200 |
25,50 |
1 - 45 |
4 - 50 |
0,36 |
109 |
541 |
80,2 |
2* |
4640 |
19,00 |
2 - 55 |
3 -00 |
0,30 |
115 |
856 |
80,7 |
Цементы на основе клинкера с КН = 0,98, отбелённого в воде |
3 |
3990 |
25,50 |
5 - 40 |
8 - 00 |
0,36 |
109 |
532 |
86,9 |
4* |
3890 |
18,00 |
3 - 20 |
5 - 10 |
0,30 |
114 |
867 |
86,9 |
Цемент на основе клинкера с КН = 0,98, охлаждённого на воздухе |
5 |
3910 |
26,75 |
4 - 35 |
8 - 25 |
0,37 |
110 |
67,1 |
83,9 |
* с применением модификатра цемента
Вследствии большого содержания C3S в опытных клинкерах и низкого - C3A, полученный на их основе белый портландцемент является быстротвердеющим, устойчивым к высолообразованию, высокоморозостойким и обладает высокими декоративными свойствами.
Энергетические затраты на производство белого цемента по новой технологии значительно ниже, чем при производстве белого цемента на природных видах сырья: удельный расход электроэнергии при подготовке сырьевой смеси почти на порядок меньше, чем при приготовлении шихты для обычного цемента, удельный расход топлива при обжиге белого клинкера по мокрому способу производства находится на уровне удельног расхода топлива при обжиге обычного серого клинкера, удельный расход электроэнергии на помол белого клинкера не менее чем на 10 % ниже по сравнению с помолом белого клинкера, получаемого по классической технологии.
Заключение
Разработанная в нашей стране технология получения декоративных цементов с применением газового или комбинированного способов отбеливания клинкера ориентирована на
массовое производство дешевых цветных клинкеров и цементов светлых тонов на базе
местного сырья и может с успехом применяться на ряде действующих заводов.
В настоящее время это особенно важно для претворения в жизнь Национального проекта «Доступное и комфортное жильё гражданам России», предусматривающего ускорение решения жилищной проблемы в стране. Важно и для создания выразительных элементов современной архитектуры в виде ярких, белых и цветных стен зданий, окрашенных долговечными декоративными цементами и для снижения стоимости их отделки. Стоимость лицевой отделки бетонных панелей с применением декоративных цементов в виде покрасок, а не традиционной штукатурки, в несколько раз дешевле стоимости отделки кирпичом или ковровой керамикой. При современных масштабах строительства в стране годовая экономия может составить сотни миллионов рублей.
1. Череповский С.С., Алёшина О.К. Белый и цветные портландцементы. // Цемент. – 1937. -
№ 1. / Бюллетень ВНИЦ. – 1937.
-
Череповский С.С., Алёшина О.К. Производство белого и цветного портландцемента. – Стройиздат, М. – 1964.
-
Паримбетов Б.П. Рост цементной промышленности Казахстана. // Цемент. – 1982. - № 12. – С. 3,4.
-
Изимгалиев И. Састобе Цемент. «Белые начинают… и выигрывают». // Цемент и его применение. 2004. - № 5. – С. 18.
-
Грачьян А.Н. Исследования процесса отбеливания цементного клинкера быстрым охлаждением в воде./ Автореферат на соискание учёной степени канд. техн. наук.- Новорчеркасск. – 1955.
-
Грачьян А.Н. и др. Технология белого портландцемента. М. – 1970.
-
Пономарёв И.Ф., Грачьян А.Н., Гайджуров П.П., Зубехин А.П. Влияние минерализующих добавок на процесс образования цементного клинкера в зависимости от электроотрицательности катиона и аниона минерализатора. / ДАН СССР. – Т. 166. – 1966.
-
Пономарёв И.Ф., Грачьян А.Н., Гайджуров П.П., Зубехин А.П., Калашников А.П. Способ отбеливания клинкера белого портландцемента. / Авт. свид. № 178723. Б.И. – 1966 . - № 3.
-
Кулабухов В.А. и др. Устройство для получения декоративного клинкера. / Авт. свид. № 950002. – 1982.
-
Кулабухов В.А. и др. Устройство для получения декоративного клинкера. / Авт. свид. № 977914. – 1982.
-
Кулабухов В.А. Интенсификация процесса обжига и повышения качества клинкера белого цемента, разработка эффективных теплообменных и отбеливающих устройств. / Дисс. на соискание учёной степени канд. техн.наук. - Москва. - НИИЦемент. - 1985.
-
Акунов В.И., Завадский Г.В., Боряков В.Ф., Русаков Г.Ф. Некоторые вопросы производства декоративных цементов при помощи струйных мельниц./ Технология белого и цветных цементов. - Труды НПИ. – 1970. Т. 227
-
Кулабухов В.А., Ференс Н.И., Шелудько В.В. Авт. свид. № 417682. // Бюллетень изобретений. - 1974. - № 8.
-
Хохлов В.К., Бессмертных А.В., Шелудько В.В., Кулабухов В.А. Методика теплового расчёта кальцинатора кипящего слоя. / Труды НИИЦемента «Интенсификация процессов обжига клинкера». – 1978. – Вып. 54.
-
Кулабухов В.А., Шелудько В.В., Ференс Н.И., Бессмертных А.В.,Островлянчик В.Я., Абрамов В.К., Шубин В.И. Модернизация вращающихся печей мокрого способа производства. // Цемент. – 1985. - № 4. – С. 18 -19.
-
Чистяков Г.И., Кулабухов В.А., Комарова Н.И., Островлянчик В.А., Абрамов В.П. Комбинированный способ отбеливания клинкера. // Цемент. – 1983. - № 11. – С.9.
-
Гайджуров П.П., Голованова С.П. Проблемы ресурсо- и энергосберегающей технологии декоративных цементов. // Цемент и его применение. – 1999. - № 5 / 6. – С. 50 – 53.
-
Зубехин А.П., Голованов С.П., Кирсанов П.И. Зависимость белизны клинкера от распределения железа по фазам при неравновесной кристаллизации. // Цемент и его примнение. - № 4 – С . 33 – 37.
-
Шубин В.И., Дмитриев А.М., Жарко В.И., Шутова А.В. и др. Способ получения белого порталндцементного клинкера./ Патент на избретение № 2147016. – Опубликован 27. 07. 1999.
-
Шубин В.И., Дмитриев А.М., Шутова А.В. и др. Разработка новой технологии производства высококачественных белых и цветных цементов. / Сб. «Качество, безопасность, энерго- и ресурсосбережение в промышленности строительных материалов и строительстве на пороге
XXI века», ч. 1.: «Энерго- и ресурсо-сберегающие технологии в промышленности строительных материалов». – 2000. – Белгород. – С. 381 – 385.
|
|